Mobile Oil Treatment Unit
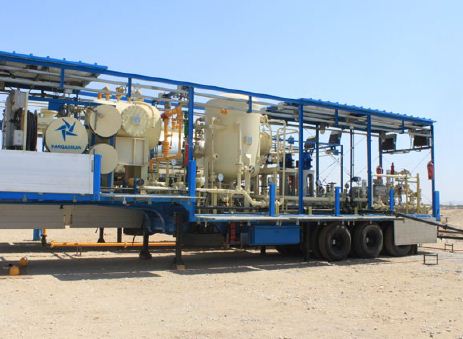
Since many large cities with significant populations are located in the oil-rich regions of southern Iran, mobile oil and gas processing services utilizing modern technologies eliminate the environmental risks associated with burning contaminated oil and gas from wells after repair, acidizing, well testing, and other operations.
After drilling, repairs, or maintenance, the produced oil is burned in pits to clean the wells and facilitate the transfer of oil to production units. However, burning oil not only causes economic losses but also leads to environmental pollution. With the introduction of mobile processing units, at least 100,000 barrels of oil per year will be saved from burning.
Application:
This device is installed on wells facing pressure loss due to issues such as sand, water, drilling mud, or asphaltic materials and require maintenance.
Device Specifications:
The unit consists of a processing unit and a desalination unit, transported on four trailers:
- Trailer 1: Carries the processing unit
- Trailer 2: Carries the pumping system
- Trailer 3: Carries the power generator
- Trailer 4: Contains the control room and service units
Equipment:
Main Equipment:
- • Manifold reducer and three-phase separator (oil, gas, and water)
- • Sand separator
- • Sediment separator
- • Electric desalination unit
- • Surge tank
- • Transfer pump and backup pump
Auxiliary Equipment:
- • Chemical injection system (storage tank, mixer, injection pump) for anti-corrosion, demulsifier, and caustic soda injection
- • Instrument air supply system (air compressor, cooler, air receiver)
- • Power supply system (diesel tank, diesel pump, generator)
- • Inert gas injection system (nitrogen)
- • Mobile caravan with all necessary amenities for staff
- • Safety equipment, oxygen cylinders with masks, and a control room for monitoring pressure, temperature, and flow rate (oil, gas, and water)
Operational Capacity:
The unit can process up to 3,500 barrels per day with a flow pressure between 150 to 3,000 psi and manage sand production up to 3,000 ppm.
Processing Workflow:
After connecting the unit’s input and output to the well and the production pipeline, the oil first enters the sand separator, where anti-corrosion chemicals, demulsifiers, and caustic soda are injected. The oil stays in the sand separator for about 3 minutes at a pressure of 150 to 5,000 psi. The separated sand is collected in a sand tank for disposal. The sand tank is equipped with level, pressure control, and safety valves to prevent accidents.
The oil then flows into the three-phase separator, which separates brine from the oil (up to 20% by volume) at an operating pressure of 150 to 200 psi. The separated water is automatically removed from the system and directed to the burn pit.
Next, the oil passes through the sediment separator, where centrifugal force created by the rapid rotation of the oil causes solid particles to fall to the bottom for manual disposal. The oil is then sent to the electric desalination unit.
If the well produces sweet oil, the desalination stage can be skipped. Otherwise, the emulsified water in the oil is treated in the electric desalination unit, which has a transformer with a 380V AC input and a 17,000V DC output. The electrical fields break the emulsions due to the polarity of the water molecules, causing the water to settle at the bottom of the tank and be discharged automatically.
The processed oil is finally pumped from the surge tank to the production unit.
Economic Benefits:
In addition to protecting the environment, this device prevents the burning of approximately 100,000 barrels of oil annually, yielding savings of over 10 million dollars per year, assuming an average price of 100 dollars per barrel.